Soldadura de Magnesio y su Sensibilidad a la Corrosión
La soldadura de magnesio y su sensibilidad a la corrosión son aspectos importantes a considerar al trabajar con este metal. El magnesio es un metal ligero con muchas aplicaciones en la industria, pero también es conocido por ser altamente susceptible a la corrosión.
Aquí hay algunos puntos clave sobre la soldadura de magnesio y su respuesta a la corrosión:
- Sensibilidad a la corrosión: El magnesio es muy reactiva químicamente y tiende a corroerse fácilmente en ambientes corrosivos, como la humedad, agua salina, ácidos y álcalis. Esto puede llevar a la degradación de las piezas de magnesio con el tiempo.
- Soldabilidad del magnesio: El magnesio es más difícil de soldar en comparación con otros metales debido a su alta reactividad y a la formación de una capa de óxido protectora en su superficie. Esta capa dificulta la formación de una unión sólida durante el proceso de soldadura.
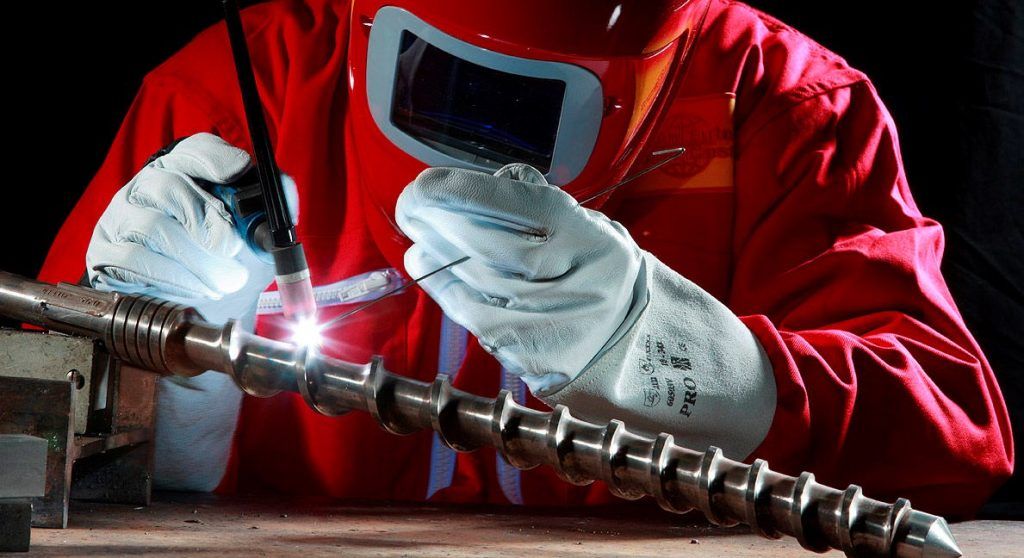
- Técnicas de soldadura: Las técnicas comunes de soldadura utilizadas para unir piezas de magnesio incluyen la soldadura por arco de tungsteno (TIG), la soldadura por arco de gas (GMAW) y la soldadura por fricción. Estas técnicas requieren un control preciso de la temperatura y la atmósfera para evitar la formación de porosidades y defectos en la soldadura.
- Protección gaseosa: Durante el proceso de soldadura, es esencial utilizar un gas de protección inerte, como argón, para prevenir la contaminación de la soldadura por oxígeno y otros gases atmosféricos. Esto ayuda a reducir la formación de óxidos y la porosidad en la soldadura.
- Preparación de superficie: Antes de soldar magnesio, es importante limpiar la superficie a fondo para eliminar cualquier óxido o contaminante. El uso de decapantes adecuados puede ayudar a mejorar la calidad de la soldadura.
- Recubrimientos y aleaciones: Para mejorar la resistencia a la corrosión del magnesio y su capacidad de ser soldado, se pueden utilizar recubrimientos protectores o aleaciones que contengan elementos de aleación como aluminio, zinc o manganeso.
- Tratamientos posteriores: Después de la soldadura, es recomendable realizar tratamientos térmicos y tratamientos de recubrimiento para mejorar la resistencia a la corrosión de las piezas de magnesio soldadas.
La soldadura de magnesio puede ser un proceso desafiante debido a su alta sensibilidad a la corrosión y su reactividad química. Sin embargo, con las técnicas adecuadas, el uso de gases de protección y la preparación adecuada de la superficie, es posible lograr soldaduras de calidad en piezas de magnesio, minimizando los problemas de corrosión y asegurando la integridad de las estructuras soldadas.
¿Qué tipo de soldadura se utiliza para soldar magnesio?
Para soldar magnesio, se utilizan varias técnicas de soldadura, pero algunas de las más comunes son la soldadura por arco de tungsteno (TIG) y la soldadura por arco de gas (GMAW o MIG).
A continuación, te explico un poco más sobre estas técnicas:
Soldadura TIG (Tungsten Inert Gas):
La soldadura TIG es una técnica que utiliza un electrodo de tungsteno no consumible para generar un arco eléctrico entre el electrodo y la pieza de trabajo. En este proceso, se utiliza un gas de protección inerte, como argón, para evitar la contaminación de la soldadura por oxígeno y otros gases atmosféricos. La soldadura TIG es especialmente útil para materiales sensibles a la corrosión, como el magnesio, ya que permite un control preciso de la temperatura y proporciona una alta calidad en la soldadura.
Soldadura GMAW (Gas Metal Arc Welding) o MIG (Metal Inert Gas):
La soldadura GMAW o MIG utiliza un electrodo consumible que se alimenta automáticamente a través de una pistola de soldadura. Se genera un arco eléctrico entre el electrodo y la pieza de trabajo, y al mismo tiempo se suministra un gas de protección inerte para prevenir la oxidación de la soldadura. Esta técnica es más rápida que la soldadura TIG y es adecuada para uniones de magnesio en láminas y componentes más grandes.
Ambas técnicas requieren una cuidadosa preparación de la superficie para eliminar cualquier contaminante o óxido, así como un control adecuado de la temperatura y la atmósfera de soldadura para evitar la formación de defectos y porosidades en la soldadura.
Es importante mencionar que debido a la alta reactividad del magnesio, la soldadura de este material puede ser complicada y requerir experiencia y habilidades específicas.
En algunos casos, se pueden utilizar otras técnicas como la soldadura por fricción y la soldadura por láser para unir piezas de magnesio, dependiendo de la aplicación y las características específicas de la soldadura requerida.
¿Qué hace el magnesio en el acero?
El magnesio en el acero se utiliza principalmente como elemento de aleación para proporcionar ciertas propiedades y beneficios específicos al material.
El magnesio generalmente se agrega en pequeñas cantidades a la composición del acero para lograr varios efectos:
- Refinamiento del grano: El magnesio puede ayudar a refinar la estructura del grano en el acero durante el proceso de solidificación. Esto puede resultar en una microestructura más uniforme y fina, lo que a su vez puede mejorar la resistencia y la ductilidad del acero.
- Desulfuración: El magnesio también se utiliza en la producción de acero para desulfurar el metal fundido. El azufre es un elemento no deseado en el acero, ya que puede afectar negativamente sus propiedades mecánicas y su capacidad de conformación. El magnesio reacciona con el azufre para formar sulfuros de magnesio, que son más propensos a flotar y separarse del metal fundido, lo que facilita su eliminación.
- Formación de inclusiones: En algunos casos, el magnesio se añade para ayudar a controlar la formación de inclusiones no metálicas en el acero. Estas inclusiones pueden debilitar el material y afectar su rendimiento en aplicaciones críticas.
- Mejora de la resistencia a la corrosión: En ciertos tipos de acero inoxidable y otros aceros resistentes a la corrosión, el magnesio puede contribuir a mejorar la resistencia a la corrosión y a la oxidación a altas temperaturas.
- Propiedades específicas: Dependiendo de la cantidad y el tipo de magnesio añadido, se pueden lograr otras propiedades específicas, como mejoras en la maquinabilidad, la soldabilidad y la resistencia a la fatiga.
El magnesio se utiliza en el acero como una aleación para mejorar diversas propiedades y características del material, desde la microestructura hasta la resistencia a la corrosión. Sin embargo, es importante tener en cuenta que la cantidad y la forma en que se agrega el magnesio pueden variar según el tipo de acero y sus aplicaciones específicas.
¿Cómo se llama la aleación de aluminio y magnesio?
La aleación de aluminio y magnesio se conoce comúnmente como aleación de aluminio-magnesio. Sin embargo, una de las aleaciones más conocidas dentro de esta categoría es la serie de aleaciones de aluminio 5000, que generalmente contienen entre un 2% y un 6% de magnesio.
Estas aleaciones son apreciadas por su combinación de resistencia, ductilidad y resistencia a la corrosión. Una aleación específica dentro de esta serie es la aleación de aluminio 5052, que es ampliamente utilizada en aplicaciones marinas y de construcción debido a su buena resistencia a la corrosión y su facilidad de conformación.
Además de la serie 5000, hay otras aleaciones que también combinan aluminio y magnesio, como las aleaciones de la serie 6000, que pueden contener también silicio y otros elementos. Estas aleaciones suelen ser empleadas en aplicaciones que requieren una combinación de resistencia y soldabilidad, como en la fabricación de estructuras y componentes para la industria automotriz y aeroespacial.
La aleación de aluminio y magnesio es una mezcla de estos dos elementos que se utiliza en la industria para crear materiales con propiedades específicas, como resistencia, ligereza y resistencia a la corrosión.
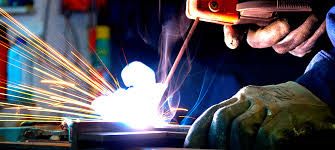
¿Cuáles son las aleaciones de magnesio?
Las aleaciones de magnesio son mezclas de magnesio con otros elementos, generalmente metales, para mejorar ciertas propiedades y características del magnesio puro. Algunas de las aleaciones de magnesio más comunes incluyen:
- Aleaciones de magnesio-aluminio: Estas aleaciones contienen aluminio como el principal elemento de aleación junto con el magnesio. Ejemplos de estas aleaciones son AZ31, AZ91 y AZ61. Son conocidas por su buena resistencia y buenas propiedades de fundición. Se utilizan en aplicaciones como componentes automotrices, piezas fundidas y componentes estructurales.
- Aleaciones de magnesio-zinc: Estas aleaciones combinan magnesio y zinc. La aleación más conocida en esta categoría es ZK60. Estas aleaciones son apreciadas por su alta resistencia y capacidad de soportar cargas dinámicas, por lo que se utilizan en aplicaciones aeroespaciales y de alta resistencia.
- Aleaciones de magnesio-litio: La incorporación de litio en las aleaciones de magnesio reduce la densidad del material y puede mejorar su resistencia y rigidez. Sin embargo, estas aleaciones pueden ser más difíciles de procesar debido a la reactividad del litio. Son de interés en aplicaciones aeroespaciales y de transporte.
- Aleaciones de magnesio-rareza: Algunas aleaciones de magnesio también pueden incluir elementos raros como cerio, neodimio y otros lantánidos. Estas aleaciones pueden tener propiedades mejoradas de resistencia a altas temperaturas y resistencia a la corrosión.
- Aleaciones de magnesio-circonio: El circonio se agrega en pequeñas cantidades para mejorar la resistencia a altas temperaturas y la estabilidad térmica de las aleaciones de magnesio.
Cabe destacar que las propiedades y aplicaciones específicas de cada aleación de magnesio pueden variar dependiendo de la composición y el proceso de fabricación. Las aleaciones de magnesio son conocidas por ser livianas y resistentes, pero también pueden ser más susceptibles a la corrosión en ciertos entornos.
Por lo tanto, la selección de la aleación adecuada depende de los requisitos específicos de la aplicación.
Deja una respuesta